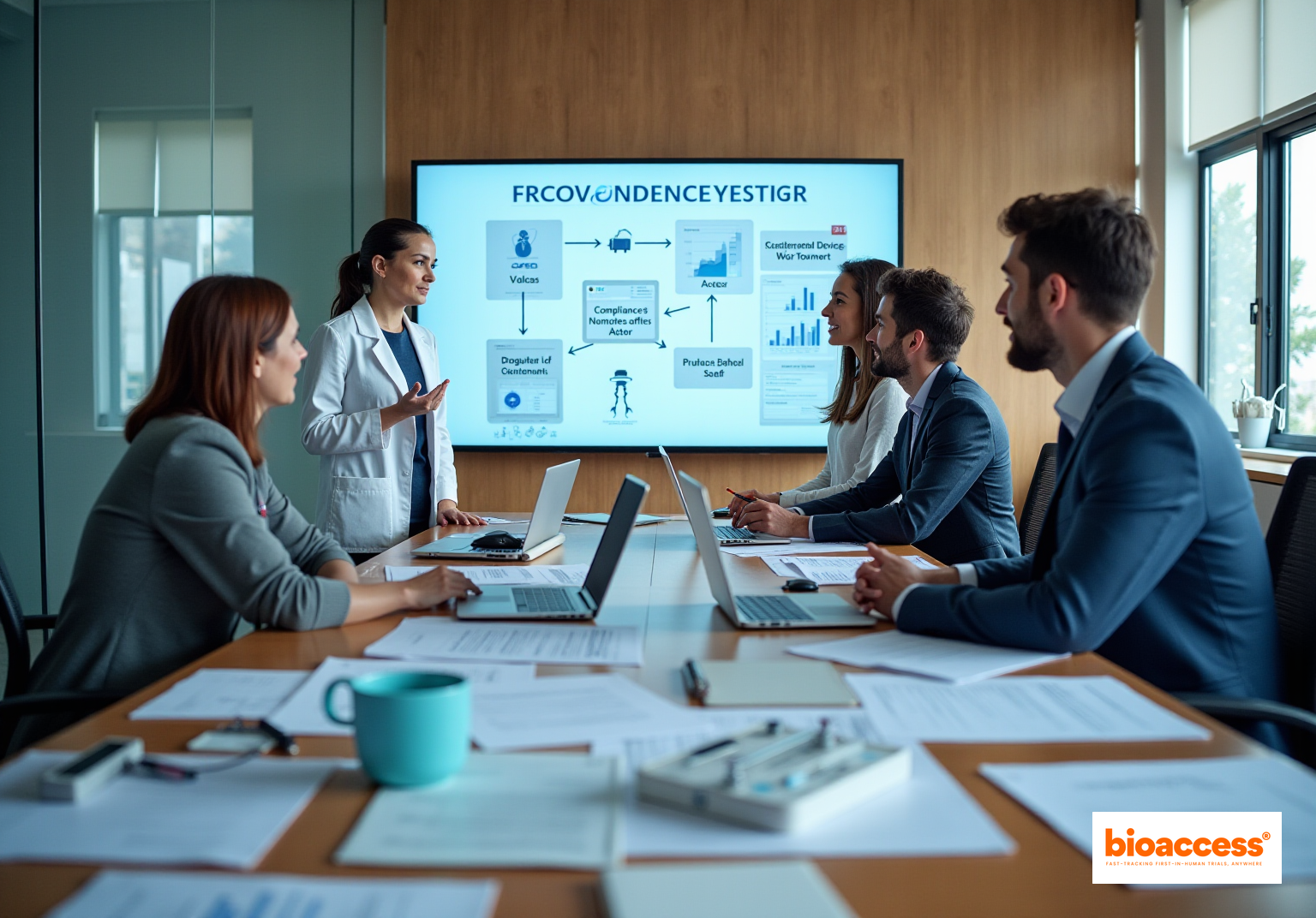
The article titled "10 Key Insights on Code of Federal Regulations Title 21 Part 820" presents essential requirements and implications of Title 21 Part 820 for medical device manufacturers. It asserts that compliance with this regulation is paramount for ensuring the safety and efficacy of healthcare instruments. This regulation mandates a comprehensive Quality Management System (QMS) that encompasses design controls, corrective actions, and thorough documentation practices. The article provides detailed explanations and examples of effective implementation strategies, underscoring the critical nature of adherence to these standards.
Navigating the complex landscape of medical device regulations presents a formidable challenge for innovators in the Medtech industry. The Code of Federal Regulations Title 21 Part 820 delineates essential quality system standards that manufacturers must adhere to, ensuring their products are both safe and effective. This article explores ten pivotal insights that underscore the critical nature of compliance with these regulations. By offering valuable strategies, Medtech companies can streamline their processes and significantly reduce time to market.
How can organizations effectively implement these standards while simultaneously fostering innovation and upholding patient safety?
bioaccess® is dedicated to accelerating adherence to the code of federal regulations title 21 part 820, which governs quality system standards for healthcare instruments. Leveraging extensive experience across Latin America, Australia, and the Balkans, bioaccess® ensures that Medtech innovators can achieve regulatory approval swiftly. This allows them to focus on innovation rather than bureaucratic hurdles. Their approach combines local regulatory expertise with global best practices, significantly reducing the time to market for new healthcare products.
With over 50 pre-qualified sites activated in under eight weeks, bioaccess® offers comprehensive clinical trial management services, including:
This end-to-end service model empowers Medtech and biopharma startups to navigate the complexities of clinical trials, ensuring a streamlined process from early feasibility studies to post-market clinical follow-up.
The code of federal regulations title 21 part 820 establishes the essential framework for a Quality Management System (QMS) that manufacturers of health-related products must adhere to. The code of federal regulations title 21 part 820 requires the establishment of a quality policy, the conduction of regular audits, the maintenance of comprehensive documentation, and the validation of all processes. Adherence to the code of federal regulations title 21 part 820 is crucial for ensuring that healthcare instruments are safe and effective for public use.
Furthermore, manufacturers must implement robust risk management practices throughout the product lifecycle to mitigate potential hazards. At bioaccess®, we prioritize information security and client trust, ensuring that our grievance and data protection procedures are transparent and compliant with applicable laws.
Should you have any queries or concerns regarding the processing of your information, please reach out to our Grievance Officer at IMH ASSETS CORP (doing business as "bioaccess®"). Our Director of Regulatory Affairs, Ana Criado, brings extensive expertise in biomedical engineering and regulatory compliance, further reinforcing our commitment to maintaining high standards in clinical trials and product safety.
The code of federal regulations title 21 part 820 outlines the Quality System Regulations (QSR), which are crucial in ensuring that medical products are consistently produced and meet safety and efficacy standards. The code of federal regulations title 21 part 820 mandates that manufacturers implement a comprehensive Quality Management System (QMS) that covers all facets of production—from design and development to post-market surveillance. By adhering to the code of federal regulations title 21 part 820, manufacturers can mitigate risks associated with equipment failures and enhance patient safety, ultimately leading to improved health outcomes.
At bioaccess, we offer a full suite of clinical trial management services, including:
These services are designed to ensure compliance with all regulatory standards, including the code of federal regulations title 21 part 820, facilitating a smoother pathway to market for healthcare products.
Establishing efficient design controls is a fundamental requirement under 21 Part 820. These controls are essential to ensure that medical devices are meticulously designed to meet user needs and intended uses. Key elements encompass:
By implementing robust design controls, Medtech innovators not only mitigate the risk of design-related failures but also significantly enhance the overall quality of their products.
Establishing robust document controls is essential for compliance with Part 21 Section 820. Manufacturers are required to implement comprehensive procedures for the creation, review, approval, and distribution of documents pertinent to their Quality Management System (QMS). This process encompasses the meticulous maintenance of records concerning changes and guarantees that all personnel have access to the most current documents. By adopting effective document control practices, organizations can significantly reduce errors, streamline audits, and ensure that all quality-related activities are thoroughly documented.
Ensuring that personnel are qualified is a critical aspect of adhering to the code of federal regulations title 21 part 820. Manufacturers must establish comprehensive training programs to identify and address the training needs of their staff. This encompasses ensuring that employees possess the necessary education, experience, and skills to perform their roles effectively. Notable specialists, such as:
exemplify the depth of knowledge required in this domain. By investing in staff training and development, companies can significantly strengthen their adherence efforts while enhancing the overall quality of their medical devices.
Implementing corrective and preventive actions (CAPA) is essential for compliance with the code of federal regulations title 21 part 820. Manufacturers must establish robust procedures for identifying, investigating, and addressing nonconformities within their processes. This includes thorough documentation of root causes and the execution of corrective actions to prevent recurrence. Effective CAPA management not only enhances quality systems but also ensures ongoing compliance with the code of federal regulations title 21 part 820.
Notably, companies that have successfully integrated CAPA procedures report a significant reduction in nonconformities, with some achieving a decrease of over 30% in reported issues. Quality assurance leaders assert that a proactive approach to CAPA can lead to improved product quality and heightened customer satisfaction, ultimately fostering a culture of continuous improvement within organizations.
By prioritizing CAPA, manufacturers can adeptly navigate the complexities of regulatory compliance while simultaneously enhancing their operational efficiency.
Conducting acceptance activities is crucial for compliance with Title 21 Part 820. These activities, which include inspections, tests, and various verification processes, are designed to ensure that medical instruments meet established acceptance criteria. Manufacturers are required to implement procedures for receiving, in-process, and finished device acceptance as mandated by the code of federal regulations title 21 part 820 to uphold product quality and safety.
By diligently executing these acceptance activities, companies can significantly reduce the risk of nonconforming products entering the market. With insights from experts like Ana Criado, Director of Regulatory Affairs and a consultant with extensive experience in biomedical engineering and regulatory practices, organizations can adeptly navigate the complexities of FDA regulations, thereby ensuring adherence to stringent quality standards.
Handling nonconforming products is not merely a regulatory requirement; it is a critical mandate under Section 21 Part 820. Manufacturers must establish robust procedures to identify, document, and control products that fail to meet specified requirements. This process encompasses thorough investigations aimed at uncovering the root causes of nonconformities, alongside the implementation of necessary corrective actions. By adeptly managing nonconforming products, companies not only ensure patient safety but also uphold the stringent regulatory standards that govern the Medtech landscape.
Maintaining comprehensive records is an essential requirement for compliance with Title 21 Part 820. Manufacturers must guarantee that all records associated with their Quality Management System (QMS) are precise, complete, and easily accessible. This encompasses documentation of:
By adopting effective record-keeping practices, organizations can streamline audits, demonstrate compliance, and uphold the integrity of their quality management systems.
Adhering to the Code of Federal Regulations Title 21 Part 820 is vital for ensuring the quality and safety of medical devices. This regulation establishes a comprehensive framework that manufacturers must follow to maintain a robust Quality Management System (QMS). By understanding and implementing these guidelines, Medtech innovators can streamline their processes and focus on delivering effective healthcare solutions.
The article highlights several key requirements, including:
Each of these components plays a crucial role in ensuring compliance and enhancing product quality. By leveraging services like those offered by bioaccess®, manufacturers can navigate the complexities of regulatory compliance more efficiently, thereby accelerating their time to market.
Ultimately, embracing the principles of Title 21 Part 820 not only fosters a culture of quality and safety within organizations but also enhances patient trust in medical devices. As the industry continues to evolve, staying informed and compliant with these regulations will be essential for Medtech companies aiming to succeed in a competitive landscape. Taking proactive steps towards compliance can lead to significant benefits, including improved operational efficiency and better health outcomes for patients.
What is bioaccess® and what does it offer to Medtech innovators?
bioaccess® is dedicated to accelerating adherence to FDA Title 21 Part 820, which governs quality system standards for healthcare instruments. It offers comprehensive clinical trial management services, enabling Medtech innovators to achieve regulatory approval swiftly and focus on innovation.
What services does bioaccess® provide for clinical trial management?
bioaccess® provides a range of services including feasibility studies, site selection, compliance reviews, trial setup, import permits, project management, and reporting.
How does bioaccess® help reduce the time to market for healthcare products?
By combining local regulatory expertise with global best practices and activating over 50 pre-qualified sites in under eight weeks, bioaccess® significantly reduces the time to market for new healthcare products.
What are the key requirements of Title 21 Part 820 for medical device manufacturers?
Title 21 Part 820 requires manufacturers to establish a quality policy, conduct regular audits, maintain comprehensive documentation, and validate all processes. It also emphasizes the need for robust risk management practices throughout the product lifecycle.
Why is adherence to Title 21 Part 820 important?
Adherence to Title 21 Part 820 is crucial for ensuring that healthcare instruments are safe and effective for public use, thereby mitigating risks associated with medical devices.
Who can I contact for queries regarding data processing at bioaccess®?
For queries regarding data processing, you can reach out to the Grievance Officer at IMH ASSETS CORP (doing business as "bioaccess®").
What expertise does bioaccess® have in regulatory compliance?
bioaccess® has extensive expertise in regulatory compliance, reinforced by the experience of its Director of Regulatory Affairs, Ana Criado, who has a background in biomedical engineering and regulatory compliance.
How does bioaccess® ensure client trust and information security?
bioaccess® prioritizes information security and client trust by maintaining transparent grievance and data protection procedures that comply with applicable laws.